As I said I would, here is the first few pages of constructing the septum feed. Any changes that will need to be made will be made later in another post.
N6BY has dimensions of a septum feed that he uses, his dimensions would work for this as well. This feed is converted from the RA3AQ septum feed.
Tools
Tin snips (straight blade style)
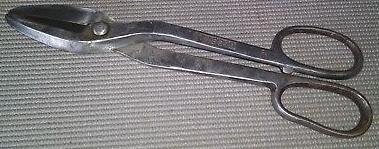
Stainless steel wire brush (must have)
Step drill
Drill bit set, includes fraction sizes
Centering punch
Pencil (something to write with)
A caliper (can use a ruler)
Mill file (8 - 10") (needle files if available)
Clamps (small quick grip and or small C clamps)
Alligator clips
Propane torch
Needle nose pliers
Screw driver (Phillips and straight blade)
Sliver based solder and 40 or more Watt soldering iron
Helping hands device (to hold part to be soldered)
Materials
4-40 S.S. screws 1/4" long
4-40 S.S. Nuts
2-56 S.S Screws 3/16" long
2-56 S.S. Nuts
2 SMA Panel mount connectors
RF Connection part #SMA-RFC19-13
3/32" Brass tube (K+S metals)
Super alloy 1 from Muggy weld (starter kit 3/32")
Aluminum parts
2 waveguide channels, 15 1/2 X 5 1/2" .040" sheet
Manufacturer for my feed parts
Puritian Mfg.
Omaha 402-341-3753
Salesman: Mike
Any metal mfgr that carries aluminum and that fabs it should be able to do this.
Building this septum feed is not a hard task but does require some hands on skills. Using of tin snips and drills along with propane torch are needed to make this feed. Cost is dependent on the tools and materials that are already available. The more you have already, lower the up front cost. Most dimensions are standard but there are some in decimal format. If one needs a decimal conversion
chart you can find it here.
Conversion chart
The basic cost for the septum materials are $85.00 or near this. This gets the basic parts made for the feed. This don't include any tools or solder needed to build the feed. I used Muggy weld super alloy 1 for the solder on this. The reason I used this is the low temp needed to melt
the solder at 400 deg F. There's other rod out there that melts at 800 deg F. but this heat will distort the thin aluminum material. If you are good at using it then by all means use it, but I don't recommend it. The low temp solder is fine for this job and high strength is not needed.
All holes drilled are pre punched first so that the drill bit don't wander from the hole. The punch I used is a metal pencil scribe that has a hardened sharp tip that makes an easy dimple in the aluminum for the starting of
drilling. I start with a small drill bit then when the hole is made in the material I go to the size I want for the final size.
The first step is to study the dimensions sheets so that you are familiar with them. Read through this manual as well to get familiar with the steps. This will help the assembly process move along. Once you are ready the next step is to decide which end of the channels you want to be the open end. What I did was put them together as they would be in the finished look, what I wanted was the two half's of the front to even.
If the back was off slightly that didn't bother me too much. You must also decide if you want the back plate even with the back edge or as mine set in by a 1/4". Setting it back makes the uneven half's a non issue.
in does make it a little tricky to assemble the septum and back plate as one. (later step) Once this is decided mark the crosshairs for the center pin of the connectors to be drilled using the dimensions from the drawings. Set the 2 waveguide half's aside.
Take the flat aluminum sheet (15 1/2 X 5 1/2") and mark or scribe the outline of the septum dimensions.
Start with the length of the septum then at the bottom of the sheet and work upward. There will be some excess height at the top step of the septum but that will be removed later. This sheet makes the septum and the back plate of the waveguide. The scrap parts make some of the spacers that
fit between the two half's of the waveguide.
After the septum is all marked out and everything is good then use the tin snips to cut it out.
In this picture I make my first cut length wise to separate the septum from the back plate. This cut is about an 1/8" as all are off the line made earlier.
Cutting 1/8" (open areas in the picture) makes the final cut much easier and more controllable. Set the back plate off to the side for later use.
Do the same for the other steps of the septum, making a cut for the step then cutting down from the top then remove the part. Follow with each step working up the steps until you reach the last one. Then carefully cut along the line made to get the final size. Take your time in this step as too much pressure with the snips and you'll remove more then you want. If you didn't quite get to the line in the cut then use a
mill file to finish to the final size. I don't recommend a motor tool due to the rapid removal of material that could easily take to much off.
In my cuts I found that maybe .010" of material may still be before the line so a file does the job well to remove that little bit. Or the cut didn't quite come out straight.
When you have the septum to the final size and are happy with it use the mill file to remove shear burrs and any burrs along cut edges that are sharp. Also in this step use the needle nose pliers to straighten any warped parts from the tin snips. The step corners should only have a very light file touch as you don't want to remove any material just the burrs. The above steps may be repeated a couple of times before the final product is achieved. Set part aside.