I've started some works on my Ajak. Of course, took it apart, cleaned, sanblasted, painted. Still need to find new end-switches, make Elevation and Declination adjusters. I like this motor!
It has task, for the beginning, to turn 1,8m Channel Master dish. Will think about improving of pulse-count afterwards.
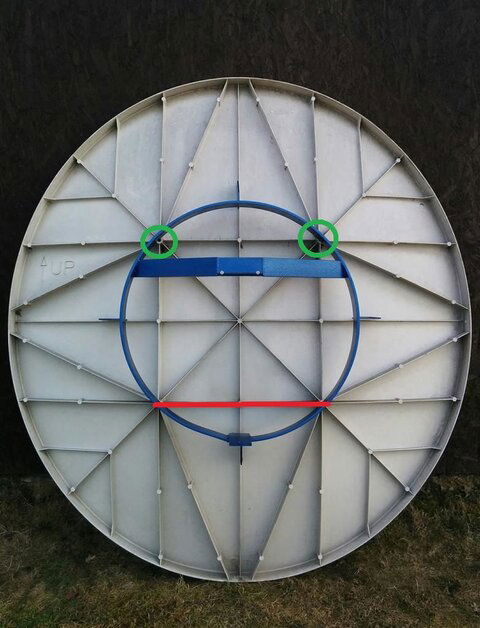

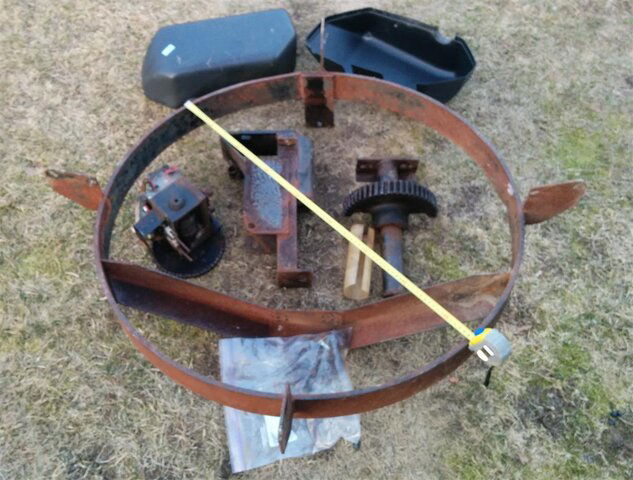
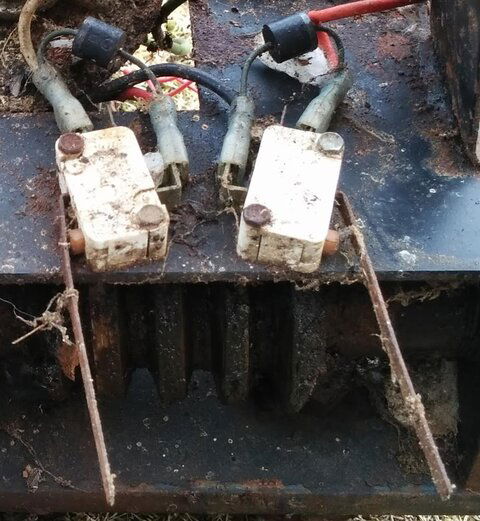
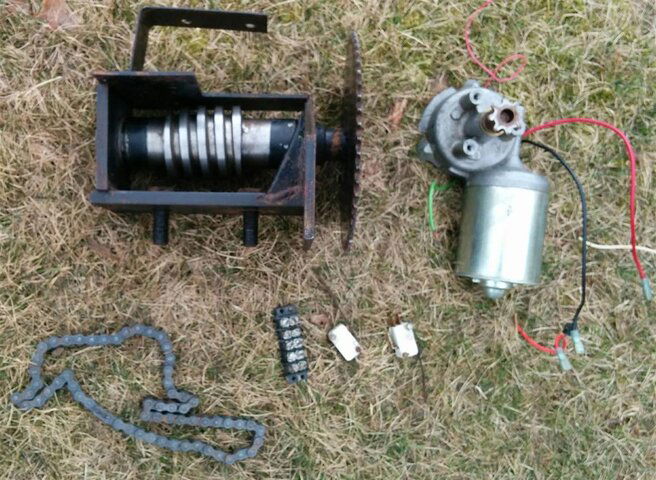
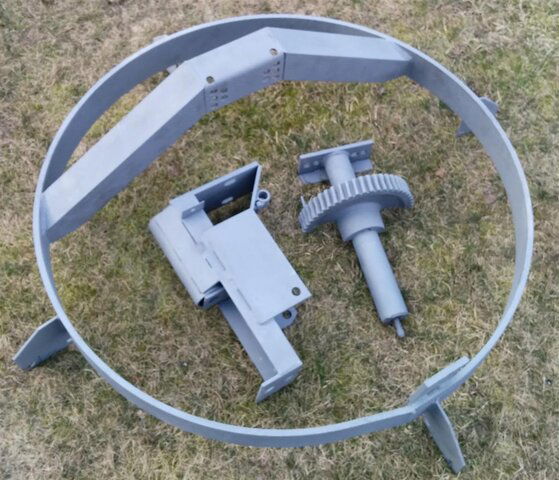
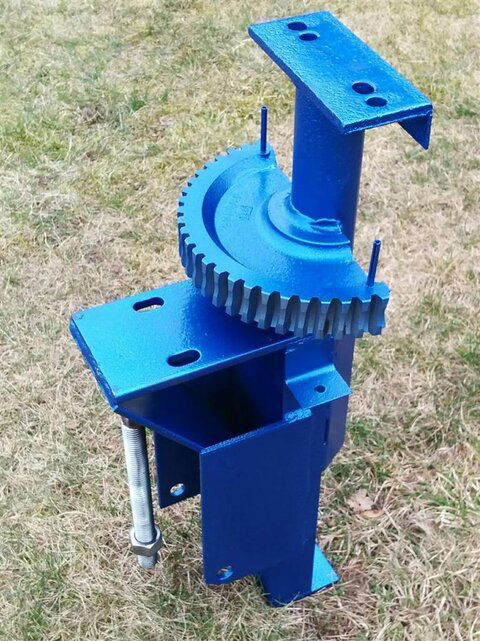
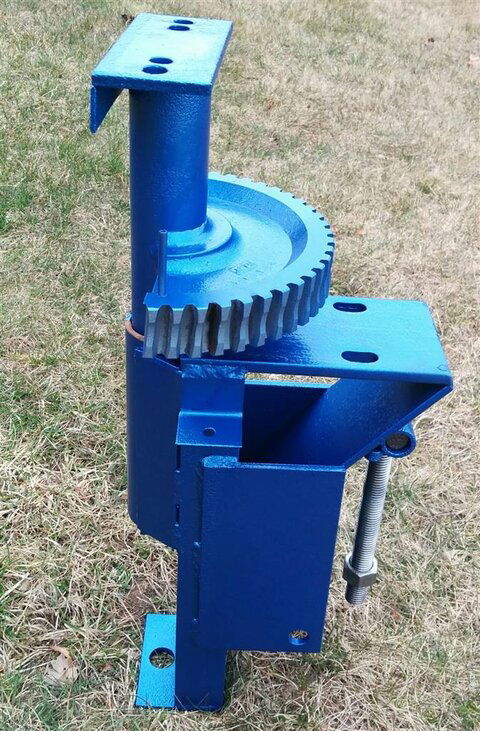
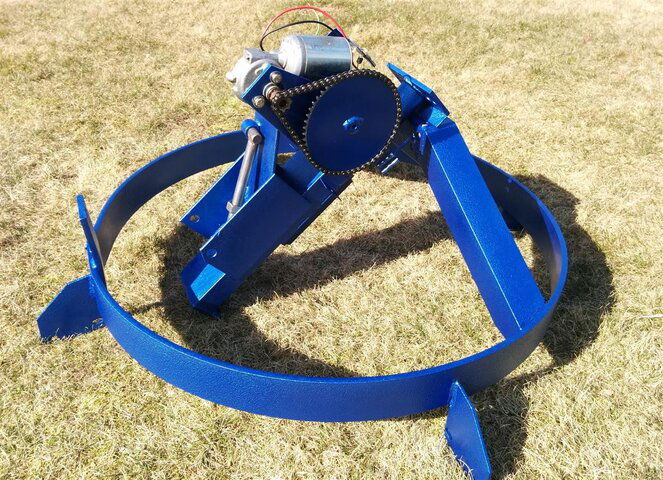
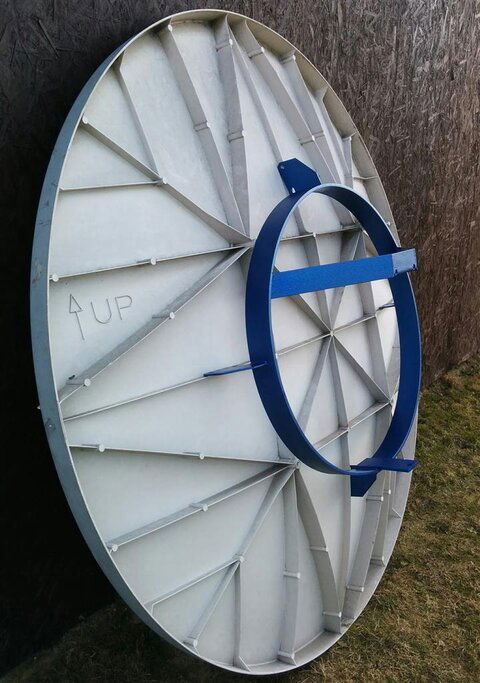
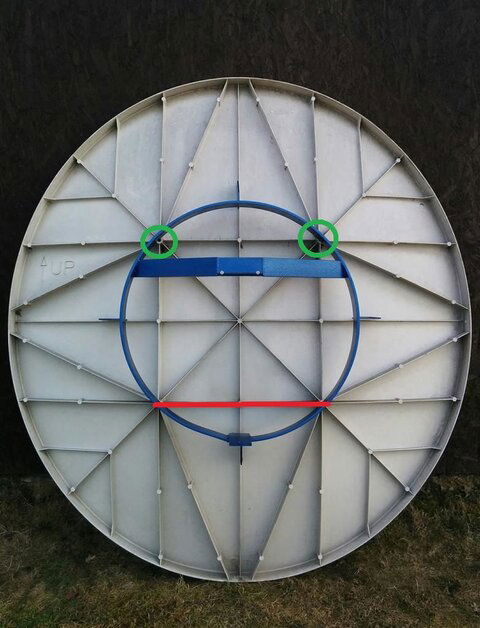